With the current labour shortages and uncertainties around shipments and the availability of raw materials, a large number of businesses are assessing their supply chains and creating/revising contingency plans. Many are now stockpiling goods to ensure they can fulfil demand, leading to the rise of just-in-case (JIC) inventory management.
The Supply Chain Crisis
A crucial part of many company’s operations, inventory management is the systematic approach to sourcing, storing and selling a company’s raw materials and finished goods. Due to the pandemic, Brexit and staff shortages, supply chains around the world are feeling the strain.
There’s a major shortfall of HGV drivers in the UK, creating bottlenecks at shipping ports and delays in goods arriving at their destinations. Additionally, the cost of shipping has skyrocketed due to a shortage of freight containers, meaning many businesses are ordering and storing more inventory than they usually would.
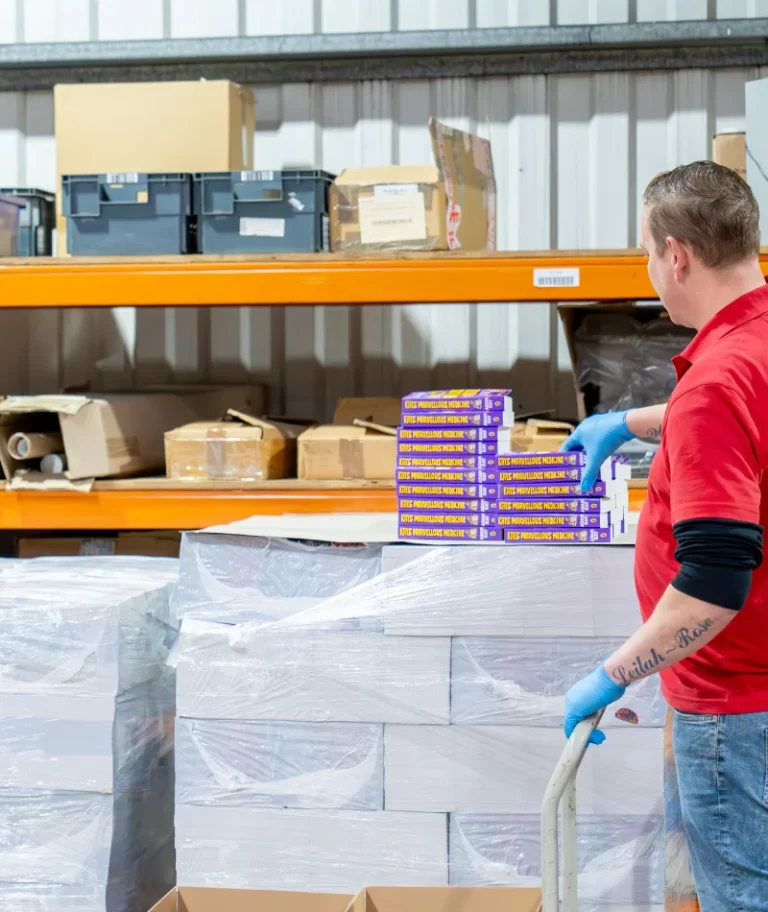
Just-in-time Supply Chains
Prior to the current supply chain issues, just-in-time (JIT) was a popular inventory management strategy used by companies looking to reduce their costs. To facilitate lean production, JIT involves only receiving the exact amount of inventory for production when it’s needed. Businesses using the JIT strategy are focused on fulfilling immediate customer demand and as such, need less storage space.
The JIT philosophy was first popularised by Toyota in the 1950s, and since then, it has been adopted by companies around the world. Certain businesses that use perishable materials will minimise waste using JIT because the materials will quickly be used in production, reducing costs.
Take a look at our Platform Integration page to see how our Inventory Management can help you.
Challenges to consider
For many businesses, the vulnerabilities of JIT have been exposed by the recent supply chain problems. If raw materials needed for production can’t be delivered due to shipping delays or HGV shortages, this could put a halt to production and lead to serious issues.
Even during times where supply is more stable, businesses operating JIT must monitor customer demand and create accurate forecasts to ensure their supply chain works efficiently. Inaccurate forecasts could lead to a company having too little inventory to meet demand or too much stock with no space to store it.
Strong relationships must also be formed with suppliers to ensure that stock is delivered on time when it’s needed. Unreliable suppliers that fail to deliver goods on time could create production delays and out-of-stock situations with the consequent impact on customer satisfaction.
Just-in-Case Inventory Management
The JIC inventory strategy is a lot more considerate of risks, keeping buffer stock just in case demand spikes or supply chain issues prevent raw materials from arriving. More stock will always be ordered before it reaches the minimum level, meaning businesses practicing JIC are more likely to satisfy demand and avoid out-of-stock situations during supply chain fluctuations.
Implementing the JIC model means that a business doesn’t have to spend as much time trying to predict demand, compared with JIT. The business can even bulk buy goods and benefit from economies of scale, reducing the cost per unit.
One of the main disadvantages of JIC is that more storage space is required, resulting in higher annual overheads. These costs need to be weighed against the costs of potentially running out of stock.
Summary
JIT and JIC inventory management strategies have positives and negatives which businesses must evaluate. To provide more resilience and stability during times of uncertainty, many businesses are combining JIT and JIC strategies in a hybrid format to ensure that they can continue operations using buffer stock if deliveries are delayed or demand rapidly increases.
If you’d like to talk to a logistics specialist about your supply chain challenges and the storage and fulfilment of your goods, please get in touch with us!